CS9500 Full Lane Survey Profiler
Two-in-One System. Collect Data Faster and With More Accuracy.
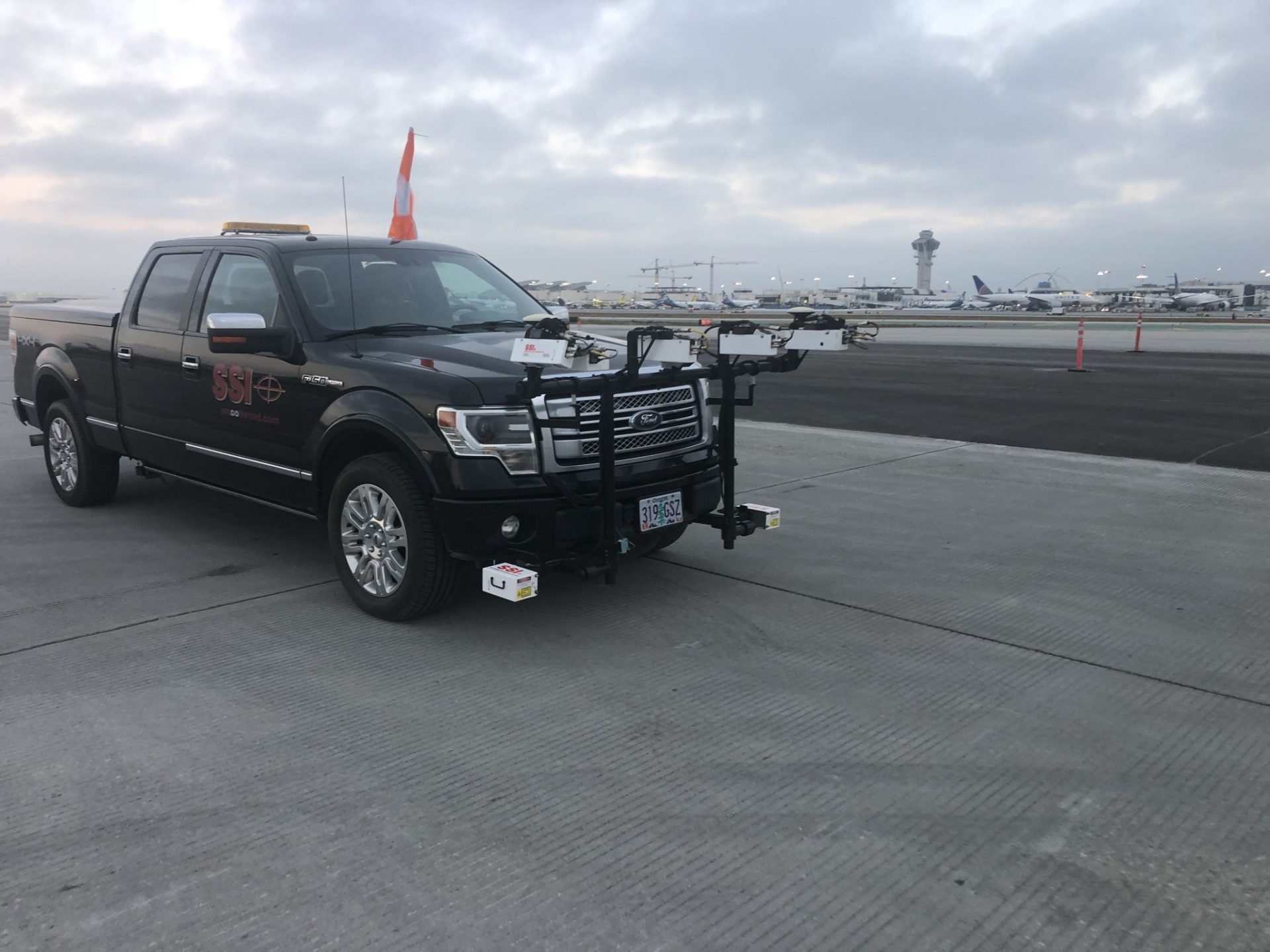
At A Glance
Top Five Reasons Our Users Prefer the CS9500:
- Two-in-One system. Inertial Profiler for IRI and Survey Scanner. Save Money. Maintain less equipment. Instant IRI Reporting.
- Only One Pass Per Lane Needed. Save Time on Collections.
- Fixed Sampling Interval at Highway Speeds.
- Zero-Speed Profiler – Collect Down to a Stop.
- IRI Based 2D or true 3D Models.
The CS9500 system has these core features:
- Collect over 9 million points per mile.
- No filtering of laser data needed. Only collect the pavement surface.
- DOT certified inertial profiler (AASHTO R56-57, ASTM E950) integrated within system and simultaneously collects data
- Zero-Speed inertial profiler to collect profile data from 0-100mph
- Typical 2″x0.5″ point cloud at 55mph (50mmx12mm at 88 kph)
- SSI CAD program to merge control points into dataset for secondary correction
- Intensity displays lane lines and delineation
- Scalable: Start with dual track profile, add cross-slope, transverse & 3D Scanning
- Supports full lane width 3D scanning and rut measurement
- SSI software merges elevation correction points for precise 3D elevations
- Outputs data in common formats (e.g.) PNEZD, PLLHD, GPGGA, and LAS
- Reusable container for storing costly sensors off-vehicle
PPK corrections and accurate sensors allow for fast collections and even fast processing. The CS9500 only needs one pass per lane.
With correction points the scan data can be corrected to be within 6mm for 95% of the point cloud. Correction points are only needed every 2,000-4,000 feet. Correction points are not needed for 2D or 2D+ differential/relative machine control models.
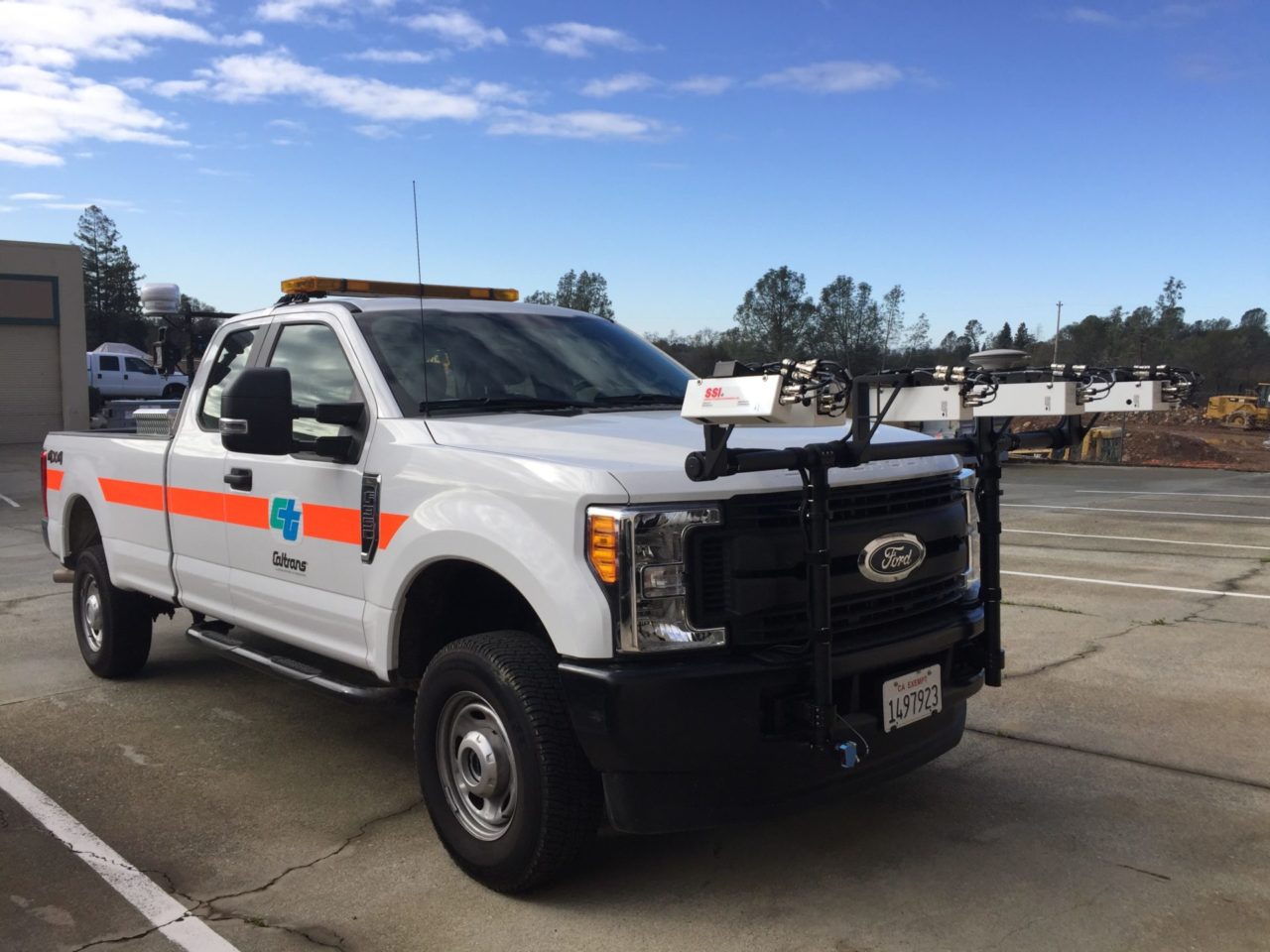
All-In-One Design
The CS9500 Survey-Profile system is both a DOT certified inertial profiler and high resolution mobile surveying system. The CS9500 can simultaneously measure IRI (longitudinal profile), transverse profile and 2D/3D surface scans for land surveying and machine control applications. The survey side of CS9500 system has been end-user validated as more accurate than any commercial vehicle scanning system. This device does full 3D scanning and can be simultaneously (or separately) used for IRI testing and full lane transverse profiles (for rutting, lane edge change and more under AASHTO PP69-10 & 70-10). The surface survey data can be adjusted with a merge in of control points for very accurate 3D elevation content.
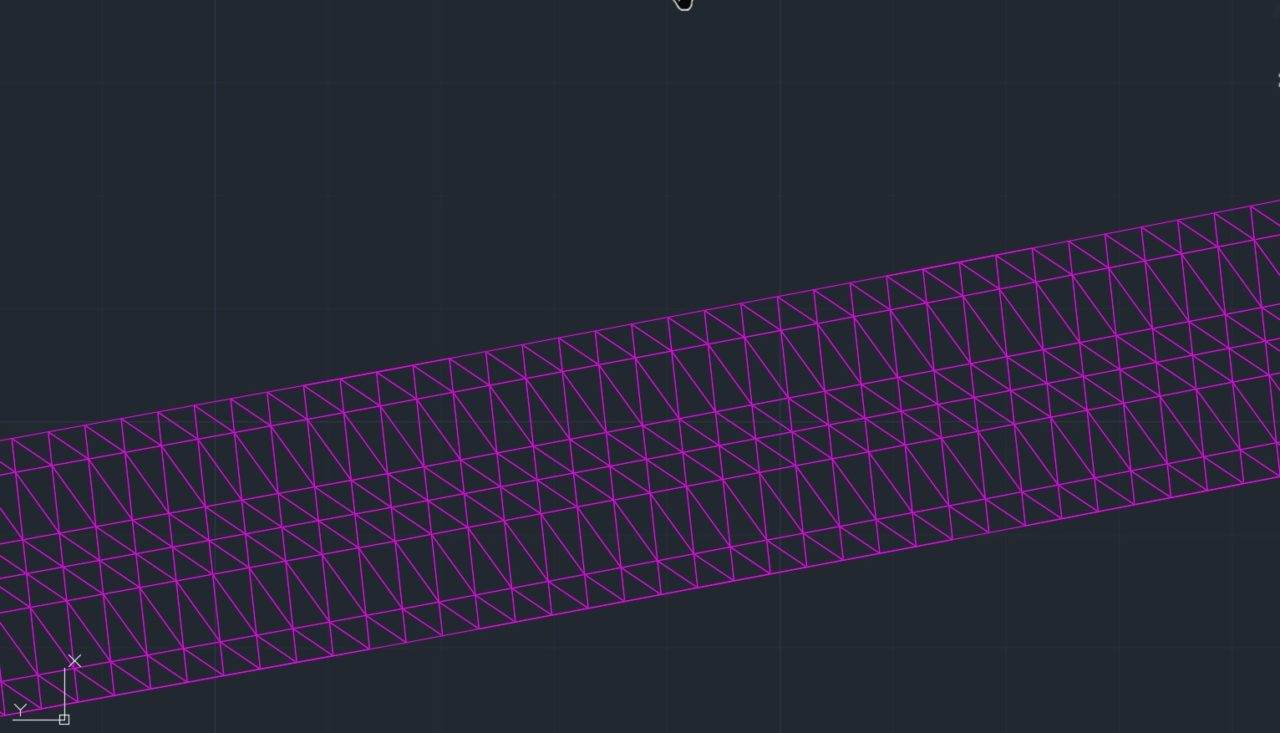
2D+ or 3D Capable
The CS9500 system can also be used for 2D scanning for pavement rehabilitation work that does not involve paving to absolute elevation. SSI’s software includes a Profile Design module for configuring slope and cut/fill parameters for a design output optimized for best IRI results. The data can be exported to machine control systems, including 2D or true 3D grade control systems.
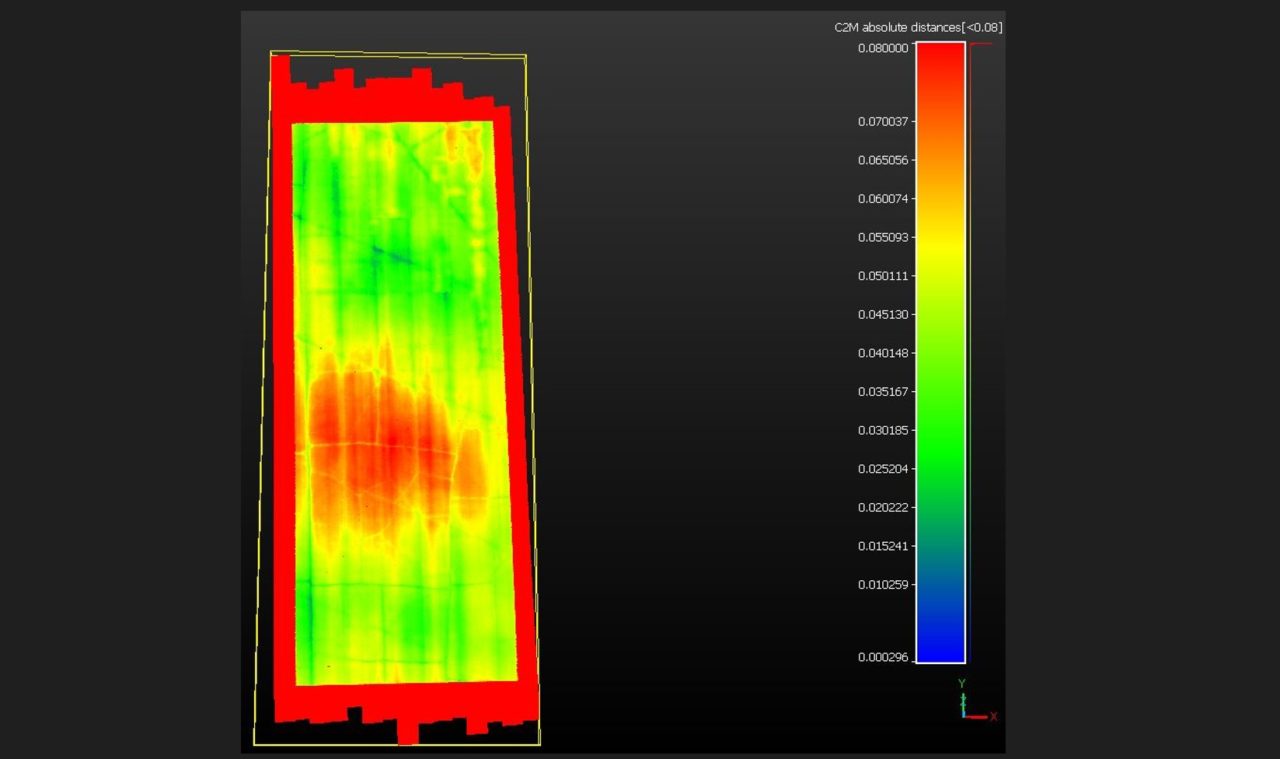
Software
The CS9500 software attributes include the following:
- Ride quality (IRI, PRI, MRI), rut depth, and cross-slope reporting
- Data compatible with ProVal
- User configurable data collection and analysis parameters
- Easy software for calibration, collection and analysis of data on in-vehicle Toughbook; software license for use on desktop PCs.
- Patented-pending process combines Inertial profiler data with IMU and corrected GPS/Control for 2D/3D surfaces.
- Dense surface data for better designs.
- Create a design file with 2D or 3D survey data in conventional survey formats, but with higher resolution.
- Use surface data in SSI Profile Design module to analyze existing surface and optimize design for best smoothness values.
- Configurable design parameters for slope, cut/fill and smoothness.
- Data compatible with third-party CAD design software.
- Design flexibility—resurvey surface to assess changes as project build progresses. Build based on the true surface profile.
- Surface designs work with both milling and paving machines.
- Separate or combined data formats: profile only, slope only, GPS only, or integrated 2D/3D survey data.
- Multiple export formats: PNEZD, PLLHD, LAS, Excel, CSV, ERD/PPF, Custom TXT & PDF.
- Precisely calculate areas of localized roughness for corrections or bonus/penalty results.
- On-screen GPS navigation along profile data.
- Surface data complies with all DOT & Industry specifications.
- Web based issue reporting and automatic software updating.
Hardware
The CS9500 hardware attributes include the following:
- DOT certified inertial profiler for IRI smoothness testing (compliant with AASHTO M328, R054, R056-057 ASTM E-950, and state/provincial agency specifications).
- Scalable: Add transverse profile system for rut depth and other measurements under AASHTO PP69-10 & 70-10. Transverse profile measured with ultra-wide beam lasers (1280 points each across 2.3ft / 0.7m).
- 5mm x 5mm resolution possible. Typical is 2″ longitudinal and 0.5″ transverse at 55mph (50mm x 12mm at 88 kph).
- Multiple configurations available; examples:
- 2 laser track profiles, IMU and GPS for 2D relative inertial profile.
- 6 laser full lane width profile, IMU and corrected GPS/control data for highest resolution 3D Topo.
- Detachable core components minimizes risk of damage or theft.
- Panasonic Toughbook rugged operator interface computer with solid state hard drive
Correction Point Merger
The CS9500 collects data as a 2D scanning system with ~15-20mm elevation accuracy. When surveyed correction points are merged into the surface using SSI’s Survey Correction software the elevation accuracy improves within a 6mm tolerance for more than 95% of the point cloud.
Cross Slope Accuracy
The cross-slope reporting on the CS9500 is accurate and repeatable. The INS and lasers work together to cancel vehicle motion and measure the cross-slope of the road by the full lane transverse measurement – not just 3 or 5 points like simpler systems.
Profile Design
Use SSI’s Profile Design to create variable cut depth models based on smoothness profiles or cross-slope requirements. The collected surface is used to extract longitudinal lines within the wheelpaths or lane edges. These lines are imported into the Profile Design program. Operators can smooth the extracted profiles and determine the cut depth at every inch along the project. Cut depth thresholds are displayed for simple interpretation and manipulation. More IRI analysis features than other software to identify hot spots or problem areas.
Intellicut Corretive Grinding
Intellicut is SSI’s version of dynamic diamond grinder simulation. The corrective grind locations determined by Intellicut are based on the wheelbase and dynamics of the diamond grinder.
Improving on other commercially available options, Intellicut:
- Is automated. Set your grinder model and IRI threshold. The program will determine the grind locations and iterate until no grinds are left or the IRI threshold is achieved.
- Set short continuous ALR, long continuous, or fixed interval. Intellicut will grind until one or all three are in compliance.
- No need to open a 3rd party program. Intellicut is built into SSI Profiler
- The grind locations are saved in the raw data file for others to view.
- Export the final grind plan to PDF
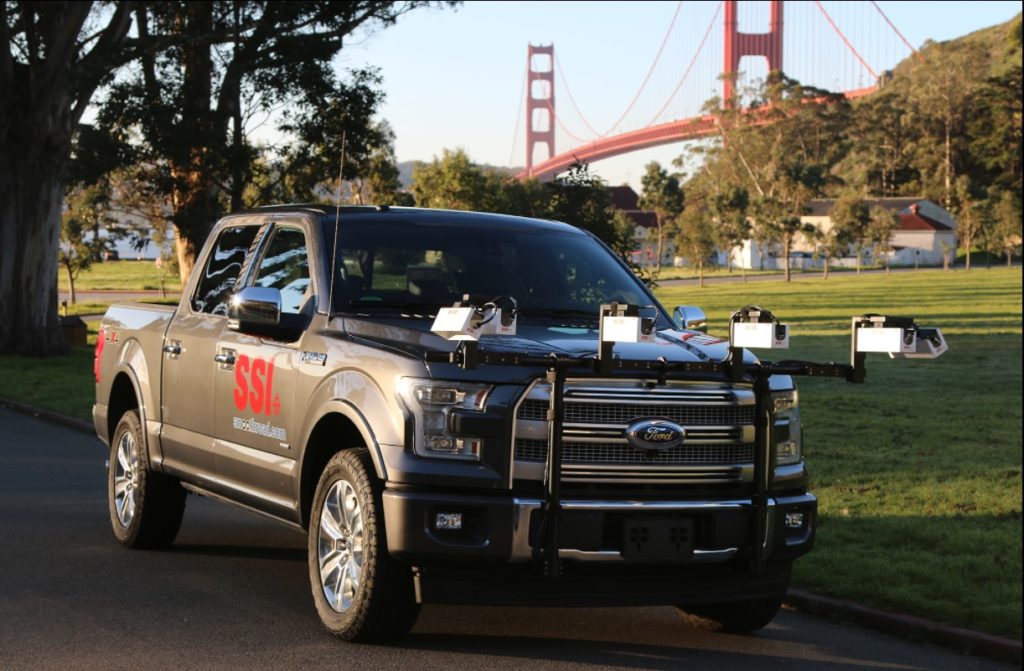
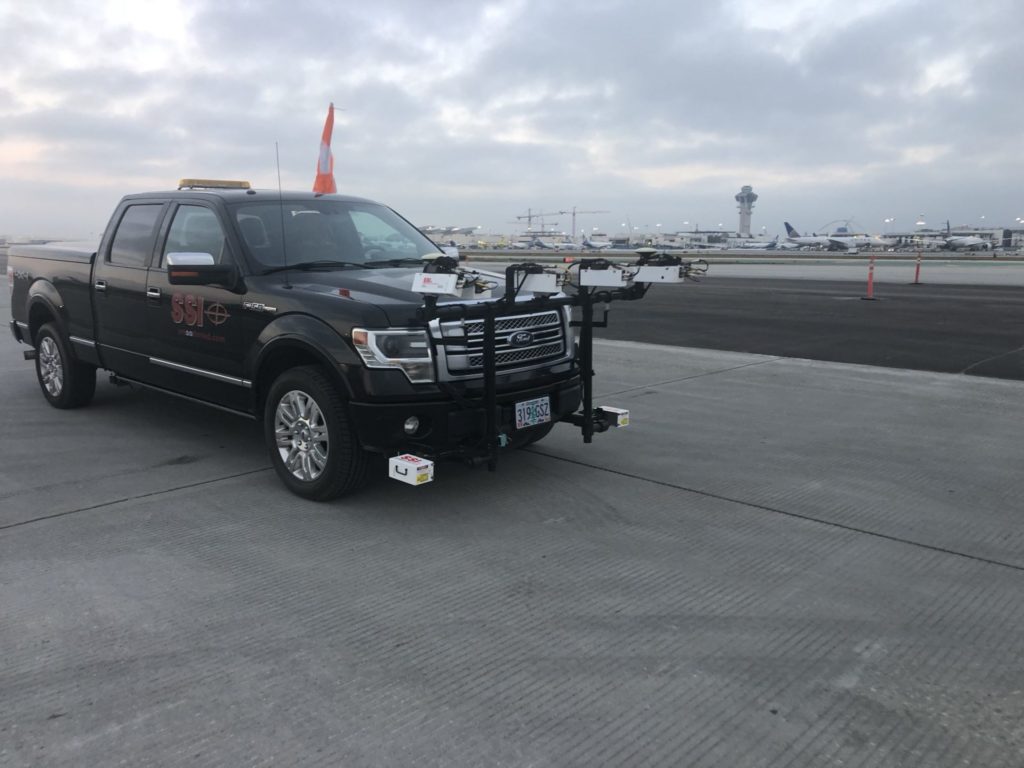
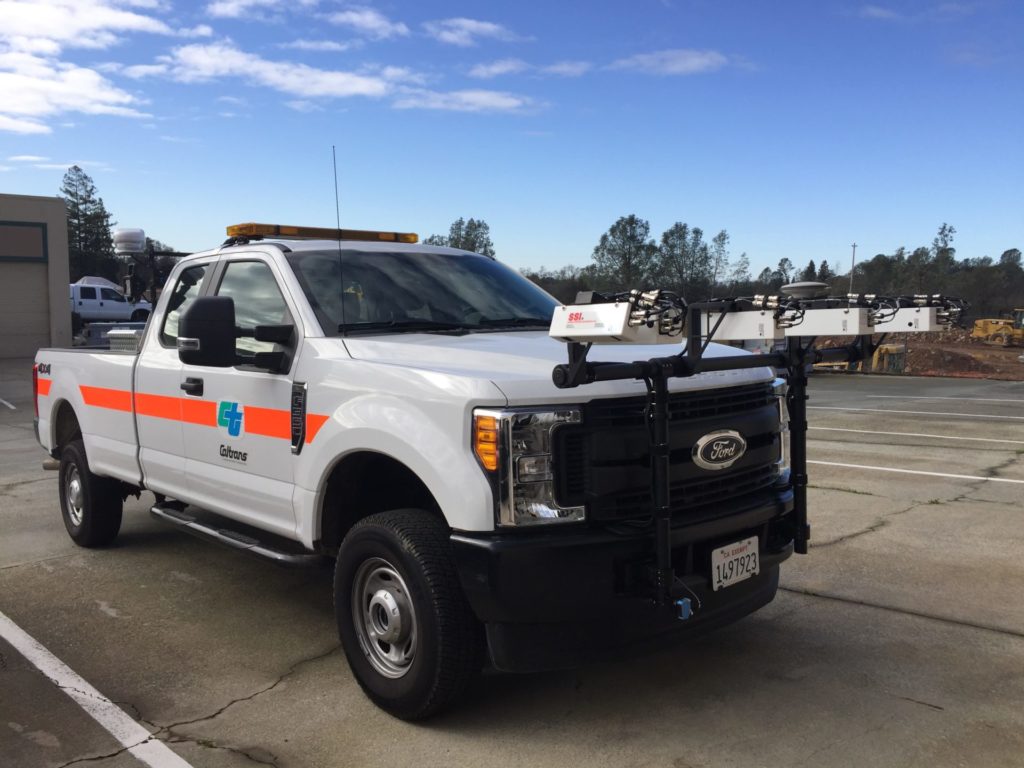
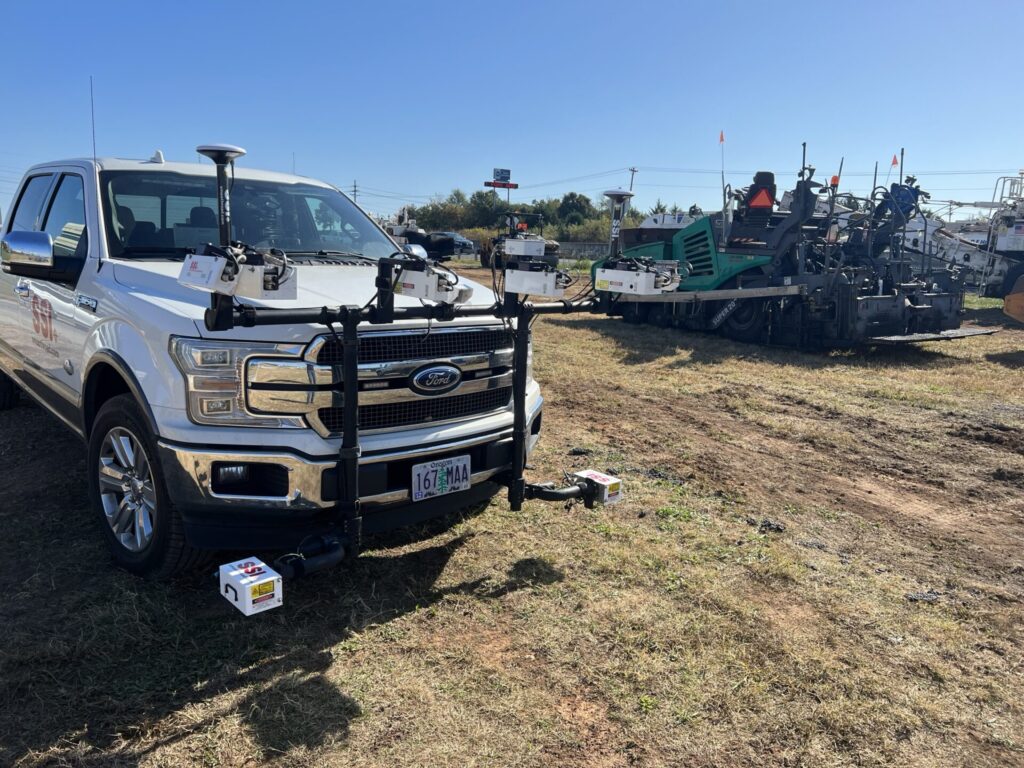
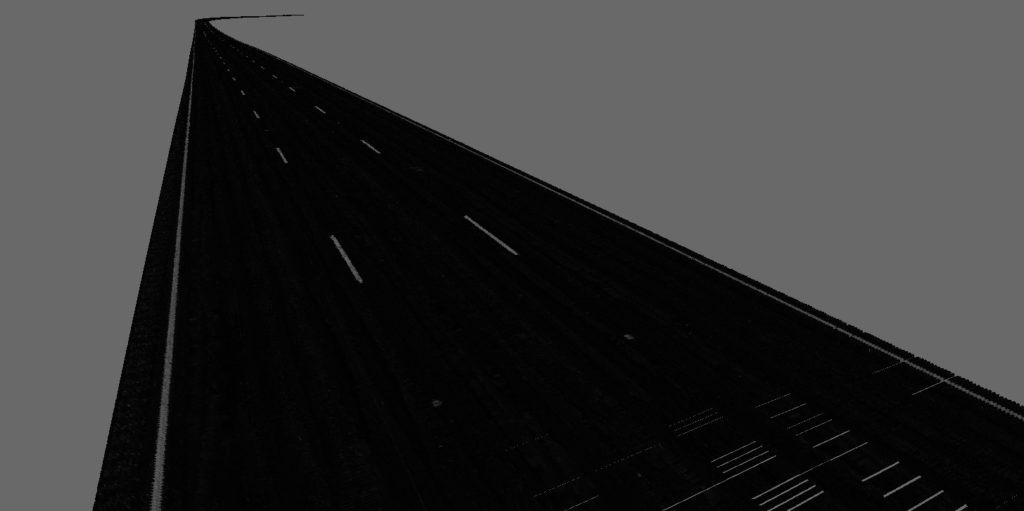
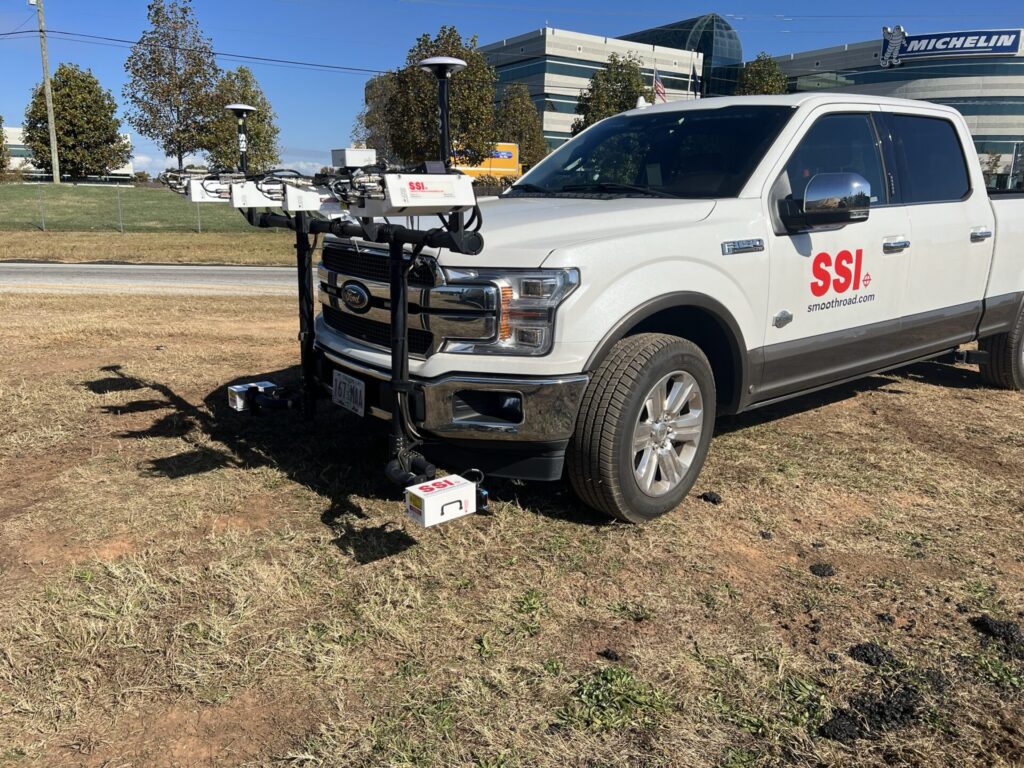
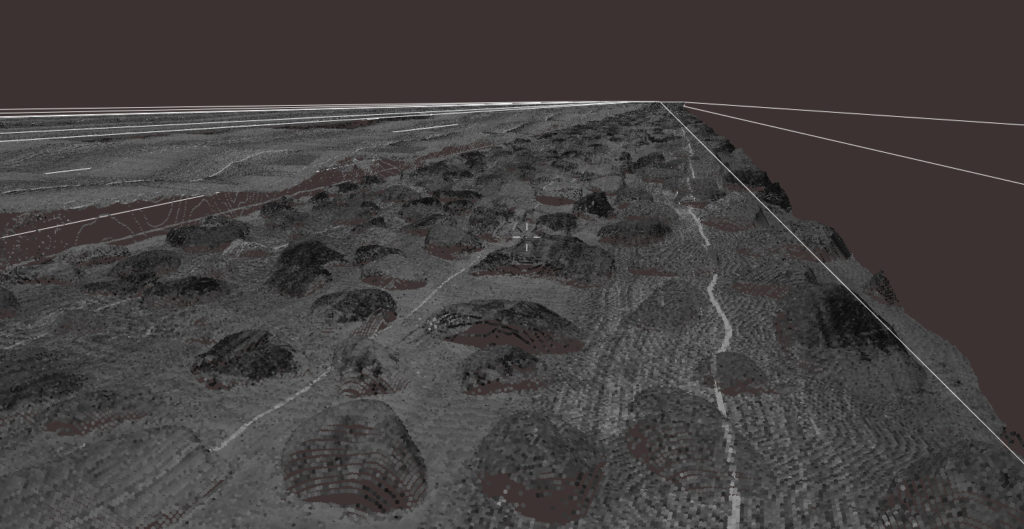
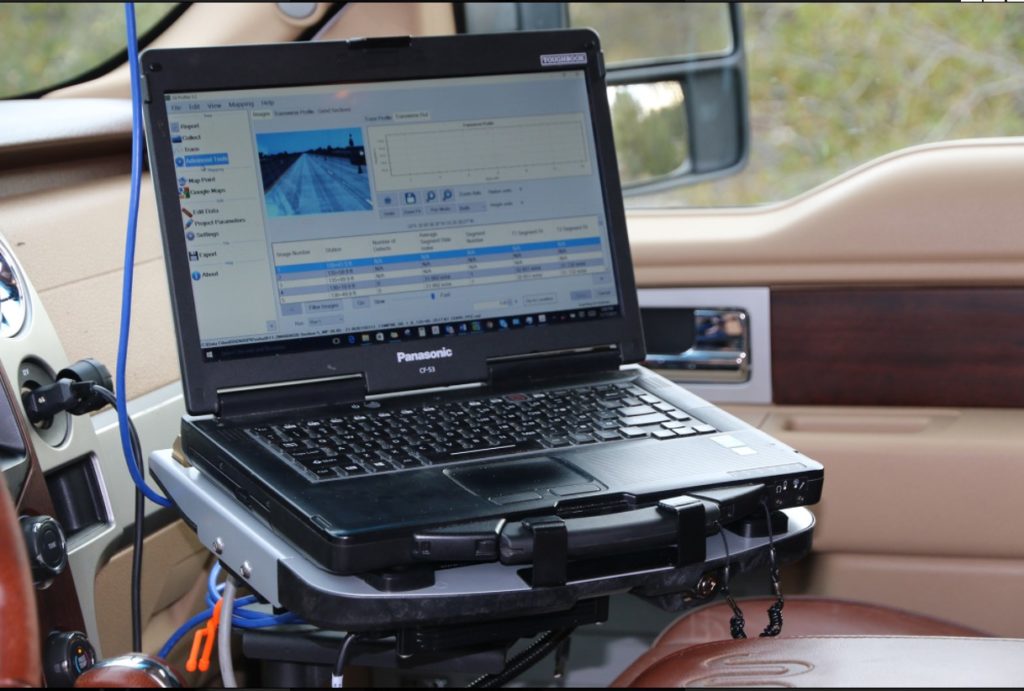
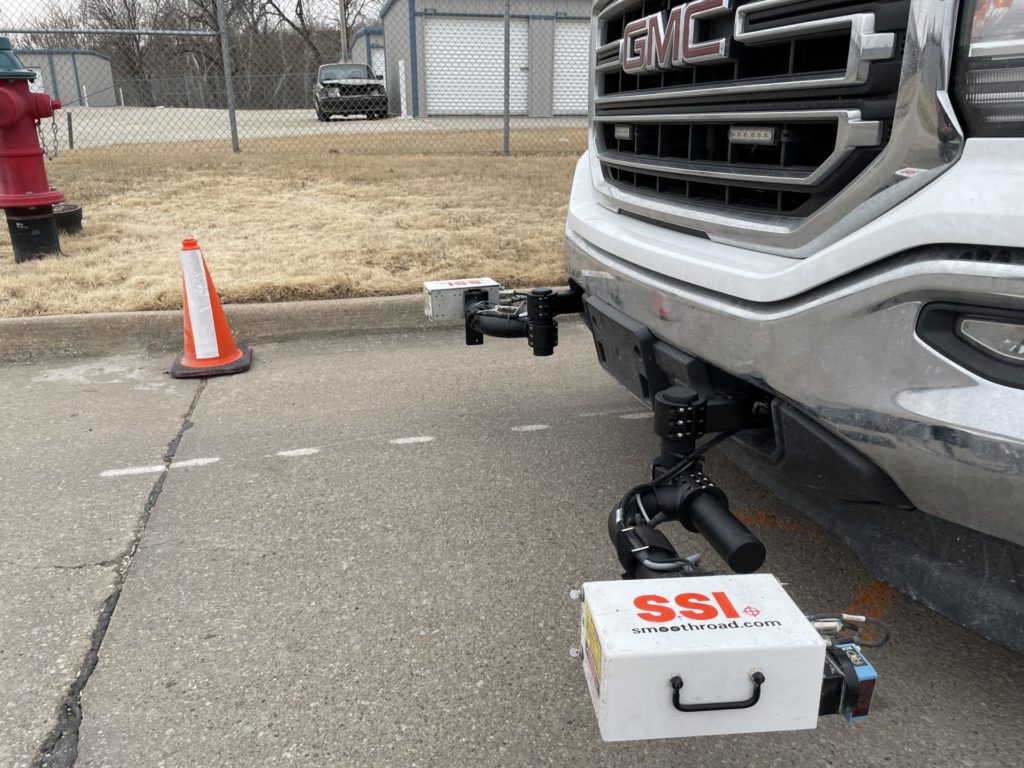
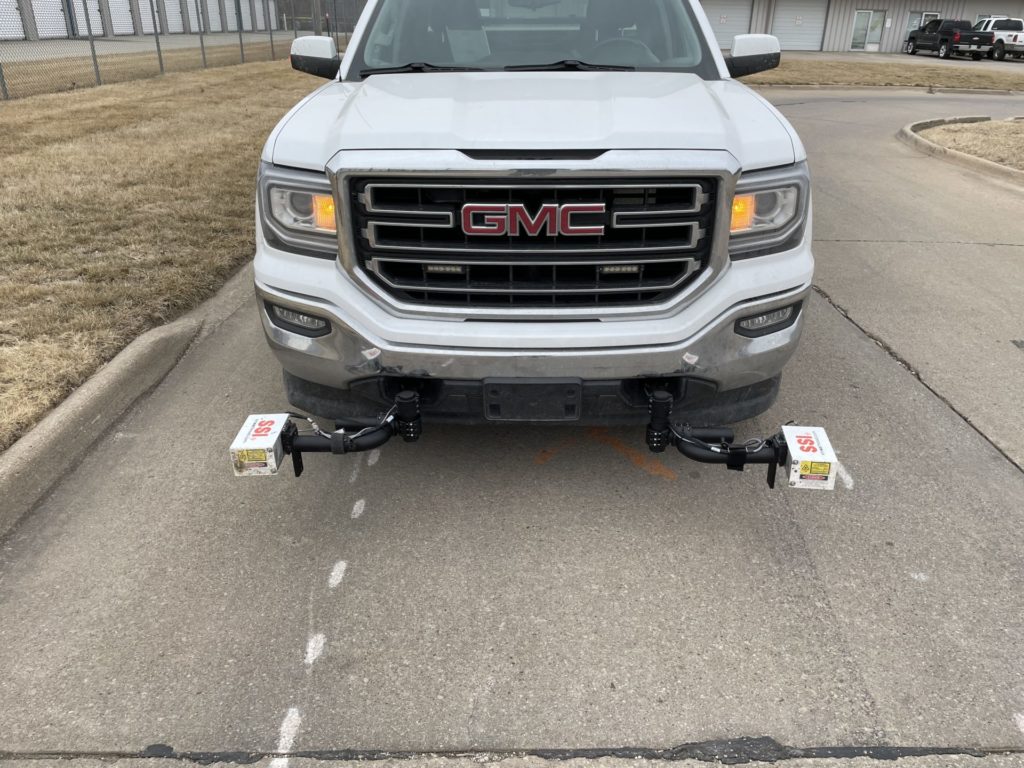
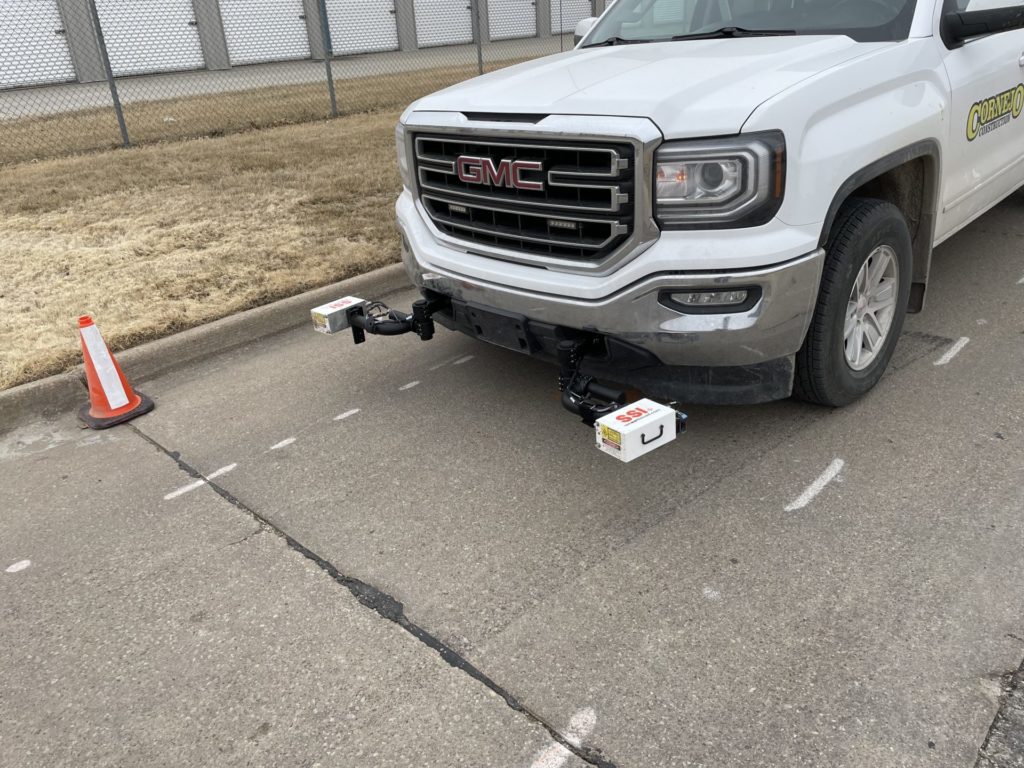